Efficient exhaust gas aftertreatment for modern machines
Weihe-GmbH offers exhaust gas aftertreatment for mobile and stationary machines in the non-road sector.
Due to successively stricter environmental regulations, a reduction in engine emissions must be ensured. However, engine manufacturers are confronted with the contradiction that a low-emission combustion process requires more fuel.
Particle or pollutant emissions can each be regulated individually via the engine. The quantity of particles is reciprocal to the concentration of pollutants. An excess of particles in the exhaust gas flow makes exhaust gas purification considerably more difficult.
The pollutants produced by the combustion process, on the other hand, can be easily reduced using chemical processes, e.g. catalytic converters or the addition of reducing agents. As a result, exhaust gas aftertreatment is required in at least one area in order to comply with legal regulations. due to the almost non-existent standardization of engines, load profiles and space requirements, suppliers of exhaust gas aftertreatment systems need to have in-depth knowledge and a holistic approach. Adaptations and developments are often the “standard”.
You can find out which exhaust gas aftertreatment your machines require on the pages for mobile and stationary machines.
Table of contents
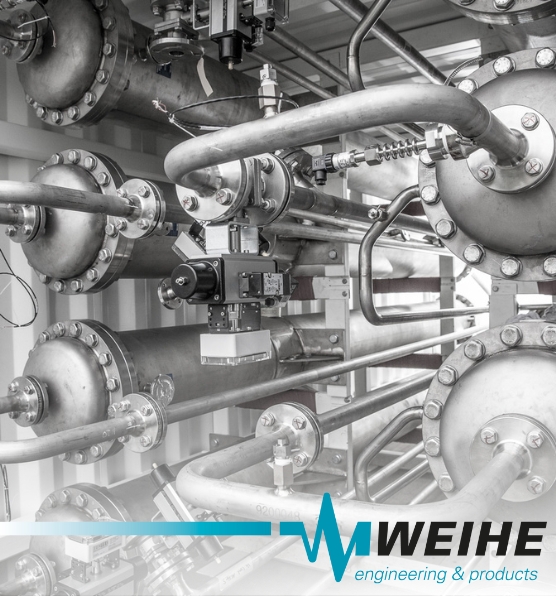
Compliance with future emission standards
Diesel engines often perform heavy-duty work, whether in construction machinery, ships or rail vehicles. The main focus to date has been on
High performance
reliability
efficiency
Another characteristic is now becoming increasingly important: in order to improve air quality, diesel engines must also be environmentally friendly.
In order to achieve this goal, the legislator has introduced binding limit values for pollutant emissions from non-road applications. These will be successively tightened over the next few years. Soot and nitrogen oxide emissions in particular need to be reduced effectively and sustainably.
The previous limit values could be complied with by optimizing the internal engine measures. Engine developers are fundamentally confronted with the contradiction that a low-emission combustion process requires more fuel.
Up to now, it has been possible to avoid both significant additional consumption and external exhaust gas aftertreatment through a high level of technical effort. However, the new pollutant limits intensify the conflict between reducing particulate and nitrogen oxide emissions on the one hand and achieving the most economical drive possible on the other.
Due to a gradual tightening, it will be an even greater challenge in future to reconcile the two. Stage IV of the emissions directive for the non-road sector is coming into force in Europe and the Tier 4 final emissions standard in the USA.
In most cases, the requirements can only be met through additional, efficient exhaust gas aftertreatment with emission control systems that have the following characteristics
Low maintenance intensity
Flawless cleaning function at sufficient temperature
Long-term performance
In this way, the contradiction between fuel consumption and emission reduction can be resolved to a large extent, as the leeway gained provides space for pure consumption optimization of the engines.
General
Weihe GmbH always offers the optimum catalytic converter and particulate filter solution for your machines and applications, regardless of the fuel type or energy source.
The use of various particulate filters leads to the reduction of pollutants such as nitrogen oxides (NOx), carbon monoxide (CO), hydrocarbons (HC), volatile organic compounds (VOCs) and hazardous air pollutants (HAP).
A wide variety of requirements are placed on catalytic converters.
- Available space
- costs
- Technical specifications
- for pollutant emissions
- for legal regulations
- customer requirements
We offer you
- NSCR catalytic converters
- SCR catalysts
- Customized solutions
NSCR catalysts
We offer you the right catalytic converter for your system. NSCR catalysts achieve a conversion of the pollutants contained in the exhaust gas into a chemically more favorable state.
Our range includes a variety of shapes and sizes to cover a wide range of engine sizes, applications and environmental conditions. The final system selection is based on the specific exhaust emissions.
To simplify the selection process, our experts will guide you through the entire project phase. This ensures that the optimum system is used.
We offer the following types of NSCR catalytic converters:
- 3-way catalytic converter
- Oxidation catalytic converter
- Diesel oxidation catalytic converter
SCR catalytic converters
The SCR catalytic converters are very efficient and work in two stages. The first stage is responsible for CO and HC reduction, while the second stage reduces NOx levels. Both stages contribute to a significant reduction in harmful emissions in order to meet the strict legal requirements. In the mixing section of the catalytic converter, either ammonia or aqueous urea is injected into the exhaust gas flow to reduce emissions.
The range includes SCR catalytic converters for the following engine types and sizes:
- From 60 KW to 15 MW
- Diesel and natural gas
Customized solutions
Do you need a customized system? – Then Weihe GmbH is your partner. Our strength lies in the analysis and solution of complex requirements.
Qualified engineers and specialists for individual solutions take on your challenge and offer you customized solutions.
Our own welding engineer ensures compliance with the necessary standards for every product. From planning and production to delivery, we guarantee top quality.
Your direct contact person will support you throughout the entire development process.
We offer you
- Professional project management
- Process-accompanying qualification
- Testing for conformity to standards
Diesel particulate filter
We offer both active and passive diesel particulate filters (DPF) solutions to remove particulate matter from diesel engines. Passive particulate filters usually use porous, ceramic wall-flow filters so that they can withstand thermal and mechanical stress during operation. If the temperature of the engine is too low, the support of an active filter (by means of thermal management [e.g. electric or fuel burner]) is required.
The design and their function are calculated so that the filter fits perfectly into any space and has long service intervals.
The filters are mounted in a modular arrangement. This special arrangement ensures that the DPF filters are stackable and can be adapted to the particle reduction capacity of the respective customer-specific requirements.
We supply diesel particulate filters for the following engine types and sizes:
- From 60 KW to 5 MW
- Diesel and natural gas